In business, non-powered assets often go unnoticed in business operations until something goes wrong—whether it’s missing equipment, costly delays, or theft. From shipping containers and industrial gas cylinders to portable sanitation units, these assets are essential for daily operations across industries. However, without visibility, managing them can feel like an impossible game of hide and seek.
By utilizing long-lasting battery-operated GPS trackers, businesses can maintain continuous oversight of these assets, even in remote or hard-to-access locations. Let’s explore some common, frustrating problems businesses face when managing non-powered assets and how GPS tracking offers more control, security, and efficiency.
Problem 1: Missing Shipping Containers – Costly Delays and Lost Goods
Picture this: a high-value shipment is on its way to a customer. Everything seems fine—until you realize the container holding your goods has been misplaced or delayed at a port. Maybe it’s sitting in the wrong warehouse, or worse, it’s been stolen.
The consequences? Missed deadlines, angry customers, and possibly lost revenue. In logistics, every minute a shipping container is off-track, the costs increase exponentially. Worse yet, companies often don’t realize something has gone wrong until it’s too late.
Solution: GPS Tracking for Real-Time Oversight
GPS tracking gives logistics companies real-time visibility into the location of every container, every step of the way. If a container deviates from its expected route or sits idle for too long, an instant alert can be triggered, allowing you to act before it turns into a costly problem. GPS doesn’t just prevent loss—it ensures goods reach their destination on time, streamlining logistics and improving customer satisfaction.
Problem 2: Industrial Gas Cylinders Gone Missing – Inventory Nightmares
For industries that rely on industrial gas cylinders—whether for medical purposes, manufacturing, or construction—keeping track of hundreds or even thousands of these cylinders is no small task. Gas cylinders are often spread across multiple locations and can be easily misplaced, left idle, or worse, never returned after use.
Without accurate tracking, businesses end up over-purchasing to compensate for missing or underused cylinders, or they experience costly downtime when the right equipment can’t be located in time.
Solution: Optimized Cylinder Management with GPS Tracking
By integrating GPS tracking into industrial gas cylinders, companies gain real-time visibility of where each cylinder is located. This not only reduces the risk of loss but also improves cylinder rotation and usage. If certain cylinders are sitting idle at one site, they can be quickly reallocated where they’re needed most, minimizing downtime and avoiding unnecessary purchases. Efficient inventory management becomes a reality with GPS, ensuring that equipment is always where it should be.
Problem 3: Portable Sanitation Units Vandalized or Misplaced – Lost Revenue and Delays
Portable sanitation units are indispensable for outdoor events, construction sites, and disaster relief efforts. But because they’re left unattended in various locations, they’re often vulnerable to theft, vandalism, or simply being forgotten. Units that go missing or get damaged lead to unexpected costs, delays in service, and frustrated customers.
For companies managing hundreds or thousands of these units, even a small percentage of lost or damaged assets can have a significant financial impact. Keeping track of where units are and when they need to be serviced is an ongoing challenge.
Solution: Protecting and Optimizing with GPS Tracking
By equipping portable sanitation units with GPS devices, companies can monitor their location in real-time and receive alerts when they’re moved without authorization. GPS tracking ensures that units are always accounted for and in the right place. This helps businesses plan for efficient service and maintenance, reducing the risk of theft or damage. With fewer lost units and better utilization, companies can improve customer service and reduce the costs associated with replacing assets.
Problem 4: Disappearing Agricultural Storage Bins – Disrupting Critical Harvest Operations
In agriculture, mobile storage bins and silos are vital for managing crops during harvest season. But when these storage units are spread across vast, remote farming properties, it’s easy to lose track of them. A misplaced or stolen bin can disrupt harvest operations, leading to inefficiencies and delays at a critical time.
Farmers and agricultural managers know the frustration of sending crews to the wrong location, or worse, discovering too late that a bin has been taken from the field.
Solution: Enhanced Asset Security with GPS Tracking
With GPS tracking, farmers gain complete visibility over their storage bins and silos, even in the most remote areas. If a bin is moved without permission, an alert is triggered, allowing for immediate action. Additionally, GPS data helps farmers position these assets in the most efficient locations for harvesting, ensuring they’re available when needed. The result? Fewer disruptions during harvest season, greater efficiency, and reduced losses from theft or misplacement.
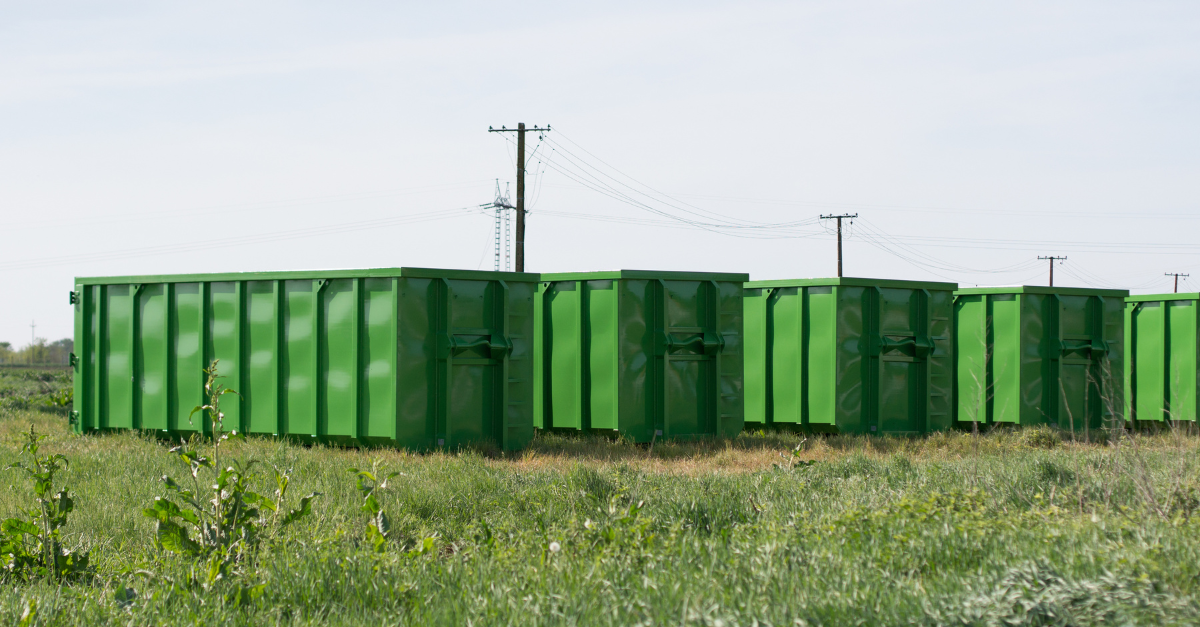
Problem 5: Waste Management Containers Misplaced – Inefficiencies in Collection Routes
For waste management companies, dumpsters, roll-off containers, and recycling bins are constantly on the move. With so many assets in circulation, it’s easy to lose track of them, leading to inefficiencies in collection routes, delays in pickups, and sometimes unauthorized use by others.
This lack of visibility can drive up operational costs, cause missed collection schedules, and even result in unnecessary purchases to replace missing or misplaced containers.
Solution: Streamlined Collection with GPS Tracking
By installing GPS trackers on waste management containers, companies can monitor each asset’s location in real-time, ensuring they are where they should be. GPS tracking helps optimize collection routes based on current container locations, improving fuel efficiency and reducing labor costs. Additionally, if a container is moved without permission, an alert is triggered, allowing for quick recovery. This means fewer lost containers, improved operational efficiency, and ultimately, a higher return on investment.
Problem 6: Modular Office Buildings Disappearing – Unexpected Losses on Remote Sites
Construction sites, mining operations, and other industries often rely on modular office buildings and trailers to provide temporary workspaces in remote locations. These assets are essential for on-site coordination, but because they’re often left unattended for long periods, they are vulnerable to theft, unauthorized use, or being forgotten once a project is complete.
The financial loss of a missing office trailer is significant—not just in terms of replacement cost, but also in terms of delayed projects and disrupted workflows.
Solution: Secure and Monitor with GPS Tracking
GPS tracking ensures that modular office buildings and trailers are secure and accounted for, even on remote job sites. By knowing the exact location of each asset, companies can ensure their trailers are moved to new sites efficiently, or flagged if they’re moved without permission. This prevents costly losses and ensures that these critical assets are always available when needed. GPS tracking offers peace of mind and reduces the risk of theft, all while keeping projects on track.
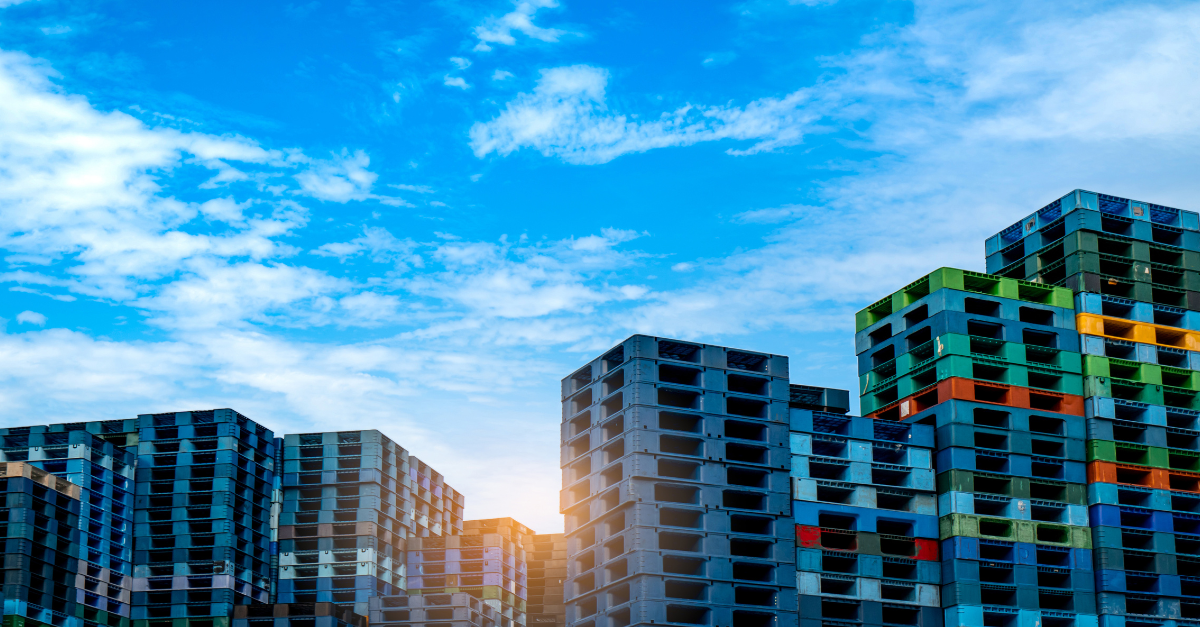
Problem 7: Shipping Pallets and Crates – Lost Assets Leading to Increased Costs
In industries such as retail, manufacturing, and wholesale distribution, shipping pallets and crates are essential for moving large quantities of goods. These non-powered assets are often shipped across long distances and multiple locations. However, pallets and crates are frequently misplaced or lost during transportation, leaving companies with additional costs for replacements, delays in the delivery of goods, and disruptions in the supply chain.
Solution: Tracking Pallets and Crates with GPS
GPS tracking allows companies to monitor the movement and location of their pallets and crates in real-time. By attaching small GPS devices to these assets, businesses can reduce the chances of them being lost or misplaced during shipping. GPS tracking ensures that pallets and crates are returned after deliveries and can be reallocated quickly for the next shipment, reducing the need for unnecessary replacements and improving the efficiency of the supply chain. This solution saves time and money, while also ensuring the smooth flow of goods.
Problem 9: Rolling Plant Carts Left Behind or Lost – Millions in Inventory Losses
Large nurseries and greenhouse operations often use rolling plant carts to transport and display plants for customers. Many businesses, however, rent these carts for short-term use and often face the frustrating issue of carts being left behind at customer locations, misplaced, or even stolen. Over time, the costs add up, and businesses can suffer from millions of dollars in losses due to missing carts. With a lack of visibility over where the carts are, replacing them becomes a constant financial drain, leaving the nursery in an unsustainable cycle.
Solution: Protecting Plant Carts with Battery-Operated GPS Trackers
To prevent further losses, nurseries have started purchasing their own plant carts and equipping them with battery-operated GPS trackers. This tracking system gives nursery managers real-time visibility over the location of each cart, ensuring they aren’t left behind or lost. If a cart is moved outside of its expected area or left at a customer’s site, an alert is triggered, allowing for quick retrieval. This solution has helped businesses not only recover lost carts but also improve overall inventory management, reducing unnecessary replacement costs and maximizing the use of existing assets. The result is significant savings and increased operational efficiency.
Problem 10: Nuclear Gauges Mismanaged – Safety Risks and Regulatory Compliance Issues
Nuclear gauges, like those used in construction and environmental testing, contain small amounts of radioactive material. These devices are critical for soil density measurements, but their radioactive nature makes them subject to strict regulations, frequent maintenance, and careful oversight. With multiple teams using these gauges across different sites, mismanagement or misplacement can lead to serious safety risks, regulatory non-compliance, or costly fines. If a gauge goes missing, it can also pose a significant environmental threat, and the company could face legal liabilities. Keeping track of these sensitive devices is crucial, but many companies struggle to maintain visibility over them during transport and use.
Solution: Ensuring Safety and Compliance with GPS Tracking
By equipping nuclear gauges with GPS trackers, companies can maintain real-time oversight of these sensitive devices. GPS tracking ensures that gauges are always accounted for, reducing the risk of them being misplaced or mishandled. Additionally, the tracking system can be integrated with alerts for scheduled maintenance, helping to ensure that the devices are serviced regularly, as required by safety regulations. If a gauge is moved without authorization or strays outside its designated area, an immediate alert is triggered, allowing for quick intervention. This ensures not only the safe handling of radioactive material but also helps companies remain compliant with regulatory standards, avoiding fines and mitigating risks to both people and the environment.
The Problem-Solver Your Business Needs
From misplaced containers to underutilized equipment, the challenges caused by a lack of visibility over non-powered assets are all too familiar across industries. GPS tracking turns these problems into opportunities for improved efficiency, better asset utilization, and reduced costs.
You no longer have to play a guessing game with your high-value assets. GPS tracking provides the real-time data and control you need to protect your equipment, streamline operations, and boost your bottom line. Whether your business is in logistics, agriculture, waste management, or another sector, GPS tracking offers the ultimate solution to transform how you manage your non-powered equipment.