The Oklahoma County Sheriff’s Office recently reported that it was missing $6.9 million in equipment, including items reported stolen and those that simply couldn’t be located. If a sheriff’s office has equipment walking out the door and never coming back, how much greater is the risk for an equipment rental company?
If a construction company loses a skid steer, they replace it and keep working. Sure, it will impact their budget and timelines, but the work they’re getting paid to do goes on. But when your core business is renting such equipment to third parties, the impact of unavailable and unaccountable equipment goes right to your bottom line. Lost, stolen, or misplaced rental equipment means you’re missing inventory, and that means lost opportunities, lost revenue, and higher operational costs.
As an equipment rental company, you also bear the risks unique to renting, such as renters who don’t return equipment or use it in an unauthorized way—including sub-leasing it out to someone else.
Asset tracking has long been a logistical challenge. Spreadsheets and manual asset tracking can only tell you where an asset should be, not where it really is. Simple automated tracking technology like bar codes or QR codes relies on physically scanning the asset. If someone isn’t standing in front of the asset with the scanner, these asset tags can’t deliver any information about the piece of equipment. They’re not very helpful tools when you need to know where assets are located outside your company’s sphere of control.
RFID (Radio Frequency Identification) asset tracking does a better job at tracking where an asset is, but only at locations where RFID readers are installed. They’re no more viable an option for the rental company than other asset tags once the rented equipment leaves the premises.
GPS-tracking has generally been associated with tracking powered assets, like vehicles or large construction or agricultural equipment. However, powered asset tracking leaves out many classes of assets that need to be tracked, particularly smaller equipment. In order to track any type of rented equipment, you need GPS-enabled, non-powered asset tracking.
Non-powered vs.
Powered Asset Tracking
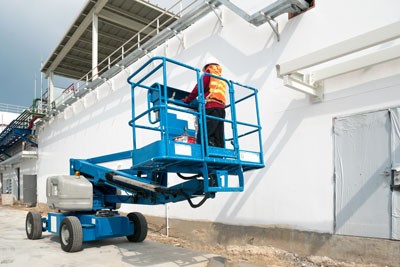
The fundamental difference between non-powered and powered asset tracking is the nature of the asset being tracked. A powered asset has its own power source, usually a battery or engine, which an attached tracking device can use as a power source. Vehicles of almost any sort are the most typical examples of powered assets. A non-powered asset has no power source, or at least no power source accessible to a tracking device. A non-powered asset can be as small as a saw or as large as a shipping container.
A powered asset tracker connects to the asset’s internal power source, either using that power to operate or to charge its own battery. Connecting the asset tracker to the asset’s power source has advantages and disadvantages:
- Because powered asset trackers are most often used to track vehicles and are connected to the vehicle’s electrical system, the tracker can also collect diagnostic data useful to vehicle fleet managers.
- The powered asset tracker may go to sleep mode when the vehicle isn’t running, to conserve the tracker’s battery life. Again, depending on the design of the powered asset tracker and its operational software, it may send location and data updates using its own battery when the vehicle is powered off. In this case, managers need to balance the frequency of data collection and delivery against the asset tracker’s battery life.
Because a non-powered asset tracker relies entirely on its own power to operate, it’s designed for long battery life. Non-powered asset trackers have batteries that can last for years or even have solar-powered batteries with an almost indefinite lifespan. Other advantages of a non-powered asset tracker are:
- They often have built-in battery power monitors, so there’s a low risk of losing contact with an asset tracker due to no power source.
- Battery replacement is easy on many non-powered asset trackers which use off-the-shelf batteries.
- With an independent power source, asset managers can configure non-powered asset trackers to collect and send valuable data on any schedule they choose. This can reduce or eliminate time gaps between updates associated with powered asset trackers when the assets aren’t actively being used.
- Based on the design of tracker and its tracking technology, a non-powered asset tracker can also capture other-than-location data that is useful to rental equipment companies in the management and utilization of their equipment (more on this below).
Because non-powered asset trackers can be used on a wide variety of equipment types, they come in a variety of sizes and installation options.
When to Use a
Non-Powered Asset Tracker
Powered asset trackers make sense for vehicle fleet managers who want them for the engine diagnostic capabilities in addition to their tracking functions. For many other companies, the larger question is what other types of equipment they should track with an asset tracker.
For a rental equipment company, the answer is simple: if you rent the piece of equipment out, you need to install an asset tracker on it. The only question is finding a non-powered asset tracker that:
- Fits discreetly and securely on each piece of equipment,
- Is built to hold up through a lot of wear and tear, and
- Can provide a full array of useful data that helps the company better manage and utilize its rental equipment inventory.
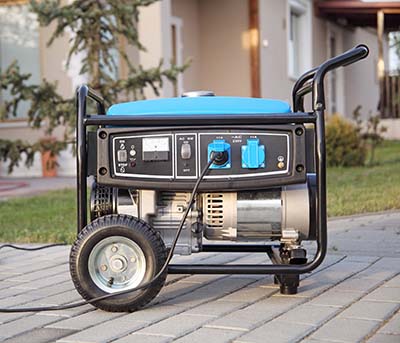
7 Ways Your Rental Equipment Company Can Use Non-Powered Asset Trackers
There are some baseline use cases that all non-powered asset trackers should meet. The asset tracker management software should provide you with a clean visual dashboard that tells you the location of every piece of rental equipment in near real-time. With the location data you can:
1. Quickly locate and recover equipment that’s reported missing or stolen, whether by the renter or from your company’s property.
2. Recover equipment that renters haven’t returned on time.
3. Improve inventory management by always knowing what equipment is available for rental and where it’s located allowing you to meet demand without delay—and without losing the opportunity to a competing equipment rental company that can act faster.
This baseline functionality saves equipment rental companies significant costs through lower insurance and operational costs of managing their equipment inventories. Relying on manual effort or scannable asset tags to locate specific pieces of equipment is costly, inefficient, and error-prone.
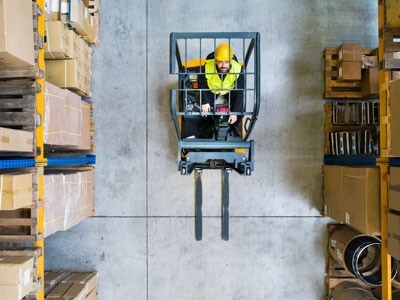
However, more comprehensive non-powered asset trackers can collect valuable information about the equipment besides just its location. Paired with a sophisticated asset tracking management software, you can also use the non-powered asset trackers to:
4. Define a geo-fence where a piece of equipment can be based on the terms of the rental contract. When a renter moves equipment outside the geofenced area, an alert can be sent to your dispatch team for immediate follow-up with the renter. Geo-fencing your equipment can help reduce unauthorized use and theft, and it can speed up recovery if needed.
6. Collect data about how and when the equipment is used by the renter to determine whether the renter has any liability for equipment damage. For example, impact detection in the asset tracker can tell you whether the equipment has been dropped or involved in a collision.
7. Identify idle and high-demand equipment to make data-driven decisions on how to grow and cull your equipment inventory. Save on storage and maintenance costs by selling off low-use equipment, while freeing up storage space and money to add more valuable equipment to your inventory.
The telematics asset tracker can collect combined with advanced, customizable management software are vital tools to establish a comprehensive asset management program. Manual asset management isn’t sufficient for managing even a small equipment inventory, and it isn’t scalable when you grow your company’s inventory. Scannable asset tags can’t track the equipment once it leaves your premises, which makes them inadequate for equipment rental companies. Many equipment rental contracts include limitations on when, where, and how the equipment can be used, which these other asset tracking options can’t begin to address.
Powered asset tracking won’t work with most of your rental equipment, making non-powered asset trackers the only viable means by which you can digitally track equipment offsite. They also provide previously unknown levels of transparency into how the equipment is handled by renters. With non-powered asset trackers, an equipment rental company has an asset management option that can help it optimize the utilization, deployment, and growth of its rental equipment inventory.
Not sure where to start? We can help answer your questions or talk to you about our asset tracking solutions.